To achieve miniaturization and high performance in camera modules, advanced packaging technologies such as Chip-on-Board (COB), Flip Chip (FC), and Wafer-Level Package (WLP) have been widely adopted in their manufacturing. These packaging techniques enhance the integration, reliability, and production efficiency of the modules while reducing manufacturing costs. Concurrently, the performance of packaging materials is continuously improving; for instance, optical packaging materials with high transparency, high refractive index, and low moisture absorption significantly enhance the optical performance of camera modules.
1. Mobile Phone Camera Packaging Materials
(1) Lens and Lens Holder Adhesive
Adhesives used for securing the lens to the lens holder primarily include low-shrinkage optical-grade UV adhesives, low-temperature rapid-curing adhesives, and UV heat dual-curing adhesives. The UV heat dual-curing adhesive is typically employed in active alignment processes (referred to as AA processes), where the AA equipment detects and positions semi-finished products for precise assembly.
(2) Lens and Lens Barrel Adhesive
Fast-curing UV adhesives are preferred for bonding the lens to the lens barrel, with requirements for high reliability under thermal shock and extreme humidity conditions.
(3) Optical Filter Adhesive
UV-curing adhesives and low-temperature rapid-curing adhesives are typically used to bond and fix the optical filter to the lens holder.
(4) Lens Holder Bracket and PCB Adhesive
Low-temperature rapid curing adhesives and UV heat dual-curing adhesives are used to bond, seal, and protect the flexible printed circuit board (FPCB) and the main PCB.
(5) FPCB Reinforcement Adhesive
Low-temperature rapid curing adhesives or UV adhesives are used for bonding the metal shell, enhancing sealing and electrical conductivity.
(6) Sensor and PCB Adhesive
Low-temperature rapid-curing adhesives are used to bond the light-sensitive chip while potting compounds are employed to enhance the chip’s reliability.
(7) Voice Coil Motor (VCM) Packaging Adhesive
Low-temperature curing adhesives are used to bond the VCM coil to its bracket, as well as to secure magnets and springs. Conductive silver paste is applied to bond, seal, and protect components such as the springs, motor terminals, and side reinforcements.
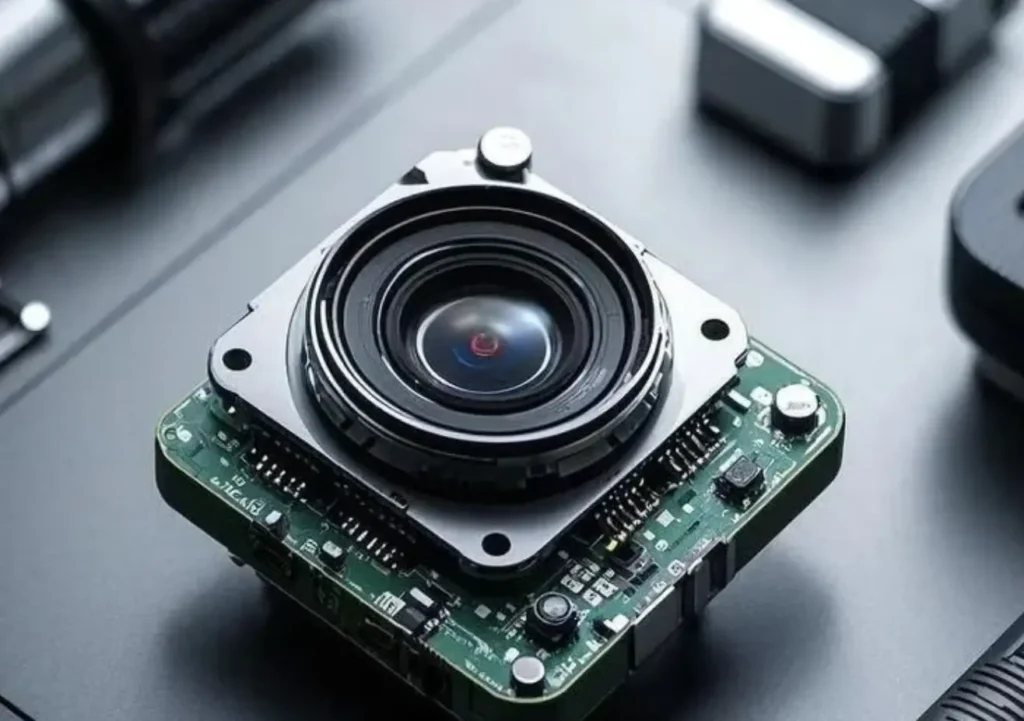
2. Automotive Camera Packaging Materials
(1) IR Filter Adhesive and Waterproof Sealing for Threaded Covers
The adhesive for IR filters requires a bonding strength of at least 3 Kg between glass and materials such as AI and PC.
(2) Waterproof Sealing for Threaded Covers
Adhesives for aluminum (AI) and polycarbonate (PC) substrates must provide a bonding strength of no less than 5 Kg.
(3) Fixed-Focus Module Adhesive
Adhesives for bonding PC, LCP, and AI should achieve a minimum torque of 8 Kg.
(4) Active Alignment (AA) Process Adhesive
For focus UV initial curing, a minimum torque of 2 Kg is required, and for secondary heat curing, the needed torque is at least 10 Kg. It is essential to maintain an appropriate aspect ratio, withstanding environmental aging from -40 to 105°C under thermal shock for 1000 hours with a torque requirement of at least 8 Kg.
(5) Lens Barrel (PPS) and Base (PBT) Adhesive
Low-temperature curing is required, with direct or lateral pull strength needed to be ≥500N after full curing. The adhesive must also pass drop tests from heights of ≥1m for at least 5 cycles while withstanding environmental aging from -40°C to 85°C for 1000 hours, maintaining a pull strength of ≥300N.
(6) PCB (FR4) and Holder (PBT) Adhesive
UV low-temperature curing adhesives are necessary. After UV initial curing, a side thrust strength of ≥200N is required. Post-secondary thermal curing needs to achieve side thrust strength of ≥500N, with a width-to-height ratio of 0.8. It must pass the dual 85 tests for 1000 hours while meeting pull strength requirements of ≥300N.
(7) PCB (FR4) and Base (PC) Adhesive
The adhesive must offer a degree of resilience post-curing, pass drop testing with ≥5 cycles for six surfaces, and endure environmental aging from -40°C to 85°C for 168 hours along with dual 85 aging for 168 hours, sustaining pull strength of ≥500N.
(8) Dust Capture Adhesive Around PCB (FR4) Chips
This adhesive must withstand thermal shock conditions from -40°C to 100°C, maintaining a cycle of temperature switching every 30 minutes for 500 cycles, with a shrinkage rate of ≤0.1%.
(9) Waterproof Adhesive for Fixed-Focus Module
The adhesive must achieve a bonding torque of ≥10 Kg with aluminum (AI) and copper (Cu) substrates after curing, while also demonstrating resistance to automotive-grade waterproof testing and enduring environmental aging from -40 to 105°C under thermal shock for 500 hours, maintaining a bonding torque of ≥8 Kg.
If you have any questions about adhesive selection and usage, please feel free to contact us. Our team of experts has extensive experience and can provide you with free consultation services.