As the demand for electric vehicles (EVs) grows, automotive original equipment manufacturers (OEMs) are prioritizing the longevity of battery packs and enhancements in power density. Adhesive solutions are essential in achieving these objectives. This article outlines how to effectively select adhesives for EV battery packs, focusing on two primary goals: battery optimization and power density.
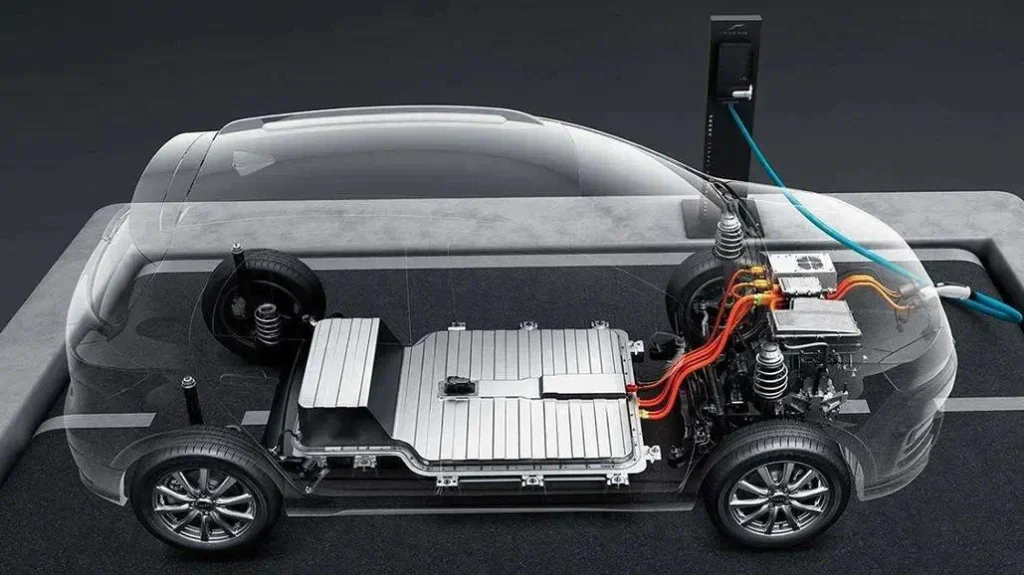
1. Key Goals for EV Battery Packs
1.1. Battery Optimization
To prolong the lifespan of EV battery packs and delay the need for replacement, it is crucial to implement technologies that ensure optimal thermal management during both operation and charging.
1.2. Power Density
Efficient power transmission from the battery pack to the electric motor is vital for rapid acceleration. Increasing power density is a primary strategy for achieving a lightweight battery design.
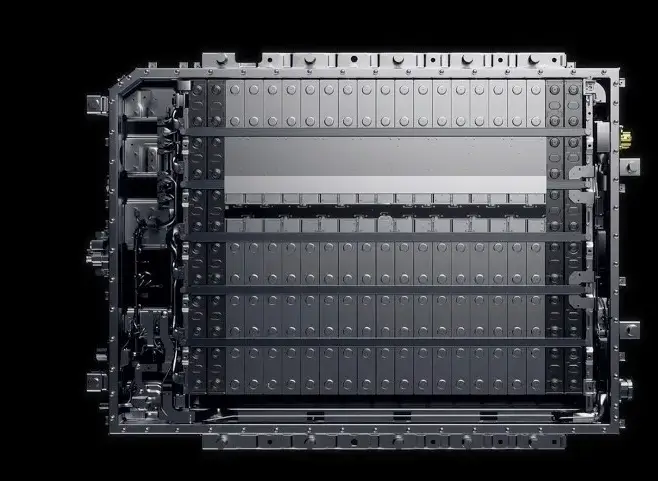
2. Bonding Solutions for EV Batteries
Vsiko, as an expert in adhesives and sealants, offers customized adhesive solutions that facilitate the assembly of EV batteries, addressing the above goals effectively.
2.1. Battery Cell Bonding
Battery cell bonding is critical for connecting individual cells within a battery pack or module. This not only ensures insulation and protection against vibration during manufacturing and throughout the battery’s life but also ensures structural integrity. Proper bonding methods may vary depending on cell type—cylindrical, prismatic, or pouch—and also helps in maintaining thermal stability while blocking impurities.
2.2. Battery Pack Structural Bonding
In the structural bonding of battery packs, various components such as modules and housings are securely joined, enhancing overall durability. Adhesives eliminate the need for mechanical fasteners, thereby reducing weight while increasing strength and rigidity. Popular choices include one- or two-component epoxies, which are applied in a precision manner to ensure optimal material utilization.
2.3. The Role of Adhesives in Battery Pack Manufacturing
When selecting adhesives, it’s important to consider their influence on the end-user experience during the operation of the EV battery pack, as well as their impact on OEM production processes.
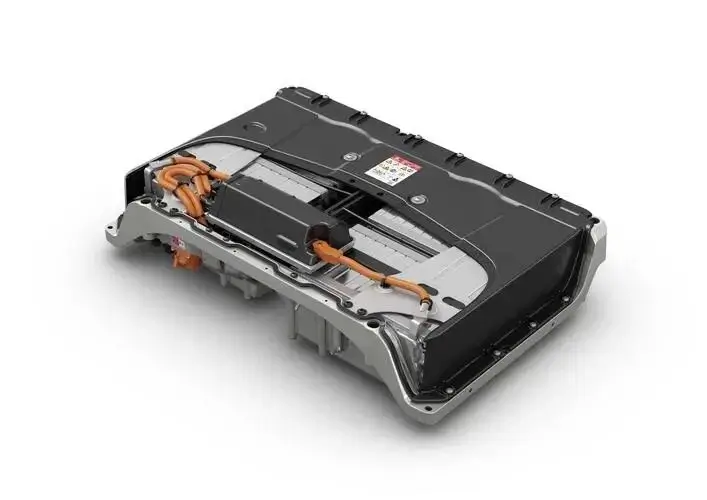
3. Performance and Handling Efficiency
3.1. Battery Pack Performance
High-quality adhesives unlock design freedom, allowing engineers to use various materials—metals, nylons, and more—to achieve peak performance. The right adhesive not only enhances thermal stability and environmental protection but also extends battery life. Thermally stable adhesives manage heat fluctuations and protect components, while robust seals prevent harmful contaminants.
3.2. Battery Pack Maintainability
The ideal adhesive can simplify repairs and maintenance for automotive OEMs. Flexible adhesives can absorb vibrations and impacts, reducing repair costs. It’s critical, however, to consider adhesive composition; those containing hazardous solvents need special handling and ventilation due to potential health risks.
3.3. Battery Pack Sustainability
Incorporating effective electrical insulation technologies allows OEMs to design battery packs with higher energy density for improved end-user performance. Electrically insulating adhesives prevent short circuits between battery cells and enable high-voltage functionality, thereby increasing operational efficiency.
3.4. How to Choose the Right Adhesive Technology
With various adhesive technologies available, understanding their unique properties is essential for selecting the best solution for specific applications. This article focuses on three primary adhesive chemistries, steering clear of traditional acrylics and epoxies for more advanced options.
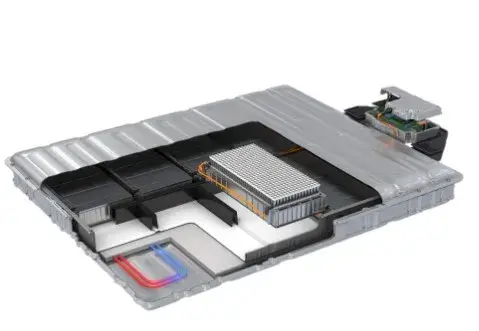
4. Adhesive Chemistries for EV Battery Manufacturing
4.1. Silane-Modified Polymers (SMP)
SMP offers primer-free bonding, broad material compatibility—effective with both metals and plastics—and flame retardancy without isocyanates for improved worker safety. Its flexibility surpasses that of traditional epoxies, managing vibrations effectively and extending battery life. SMP solutions are 100% solvent-free, making them suitable for a variety of industrial applications while aligning with sustainability initiatives.
4.2. Two-Component Polyurethane (2K PUR)
2K PUR adhesives bond a wide range of materials, including nylon, steel, and aluminum, while being odorless and flame-retardant. They offer superior flexibility and thermal expansion management. Suitable for room temperature or heat-assisted curing, these adhesives ease the joining of multiple components and promote resource efficiency.
4.3. Reactive Hot Melt Polyurethane (HMPUR)
HMPUR adhesives cure with moisture upon heating and offer excellent chemical resistance for EV applications. These solvent-free adhesives are easy to store and handle, reducing the need for special ventilation. Their flexibility during curing enhances vibration and sound absorption, promoting quieter and longer-lasting batteries.
Conclusion
Selecting the right adhesive solutions is crucial for the effective manufacturing and performance of high-quality battery packs in electric vehicles. By adhering to considerations related to battery optimization, performance, maintainability, and sustainability, OEMs can leverage advanced adhesive technologies to meet the evolving demands of the EV market.
If you have any questions about adhesive selection and usage, please feel free to contact us. Our team of experts has extensive experience and can provide you with free consultation services.