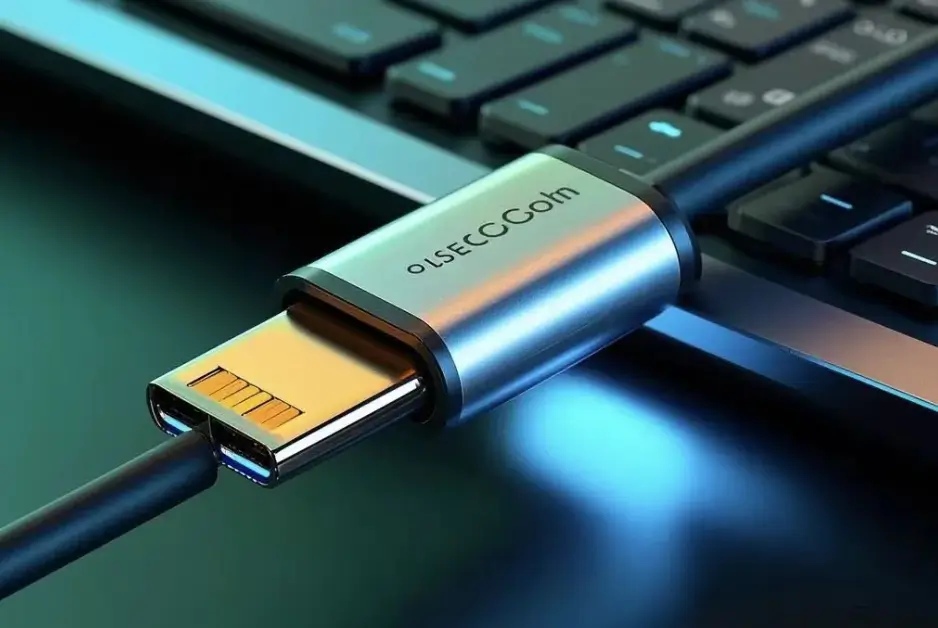
1. Type-C Development Trends
1.1 Technical Performance
(1) Faster Transmission Speeds:
With support for standards from USB 3.1 and 3.2 to USB4, future transmission speeds are expected to reach several tens of Gbps or even higher.
(2) Enhanced Charging Capability:
Higher voltage and current support will facilitate faster charging speeds, and bidirectional charging will become standard.
(3) More Compact and Flexible Design:
With advancements in semiconductor technology, sizes will continue to shrink, allowing for more versatile designs that can accommodate various devices.
1.2 Application Scope
(1) Consumer Electronics:
Type-C has become the standard connector for nearly all electronic devices, including smartphones, tablets, laptops, and monitors.
(2) Automotive Electronics:
It is used for device connections within vehicles, such as in-car entertainment systems and intelligent driving assistance systems.
(3) Industrial Applications:
In industrial scenarios, Type-C meets the high-speed data transfer and reliable power supply needs for control devices and automation production lines.
1.3 Market Trends
(1) Growing Market Size:
With the rise of emerging technologies like 5G and the Internet of Things, market demand is steadily increasing, with expectations of over 20% annual growth in the coming years.
(2) Intensifying Industry Competition:
The entry of more manufacturers into the market will intensify competition, compelling companies to maintain competitiveness through technological innovation, quality improvement, and cost reduction.
1.4 Environmental and Safety Considerations
(1) Increased Environmental Awareness:
Production processes will focus more on sustainability, with the use of recyclable materials, reduction of hazardous substances, and longer product lifespans.
(2) Enhanced Safety:
More safety protocols such as encrypted transmission and identity verification will be supported, along with features like tamper-proof and anti-counterfeiting measures.
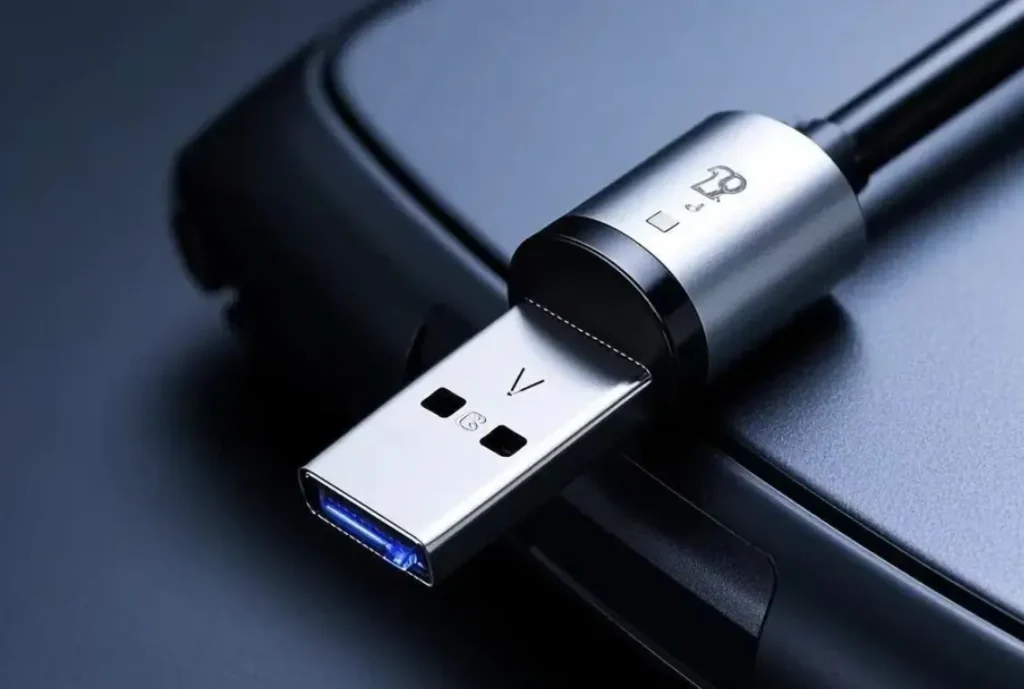
2. Type-C Packaging Materials
2.1 Performance Requirements
- Electrical Performance: Must have high insulation resistance to ensure good electrical isolation between different pins and circuits, and maintain a stable dielectric constant to minimize signal degradation and distortion during high-frequency transmission.
- Mechanical Performance: Should withstand forces from frequent plug-in and unplugging without deforming or breaking. It should exhibit good flexibility and impact resistance, and once cured, provide mechanical support with adequate hardness.
- Thermal Performance: Should have high thermal conductivity to aid in heat dissipation, and remain stable across a temperature range, withstanding extremes from 120°C to 260°C.
- Chemical Performance: Must be resistant to corrosion from sweat, cleaning agents, and meet flame retardant standards to mitigate fire risks.
2.2 Processing Requirements
- Flow and Penetration: Good flowability and penetration are essential for adhesive applications, ensuring complete coverage and uniform sealing in the gaps between Type-C pins.
- Curing Properties: Quick-curing single-component products simplify the operational process and shorten production cycles, such as single-component epoxy adhesives curing at 140°C in 18 minutes.
- Environmental Compliance: Adhesives should meet international environmental standards, minimizing halogen content and being solvent-free, with no volatile organic compounds (VOCs).
2.3 VSiKO Related Products
- High-Temperature, Humidity-Curing Silicone Gel VSi6633: Designed to meet IPX7 sealing requirements for Type-C, VSi6633 is a single-component, moisture-curing silicone sealant with excellent flowability, suitable for electronic components, end caps, and connector sealing and protection, and it withstands high/low-temperature cycles and reflows soldering up to 260°C.
- High-Temperature, Thermosetting Silicone Gel VSi6611: This product meets IPX8 sealing requirements and offers superior flow characteristics. It is ideal for applications requiring waterproofing and long-term reliability in electronic components, end caps, and connectors while withstanding temperature ranges from -40°C to 260°C.
- High-Temperature, Thermosetting Epoxy Adhesive VEP2981: Also aimed at IPX8 sealing applications, VEP2981 is a single-component epoxy resin adhesive with good flow properties, designed for electronic components, end caps, and connectors, providing waterproofing, humidity resistance, and long-term reliability under high and low-temperature cycles and reflow soldering processes.
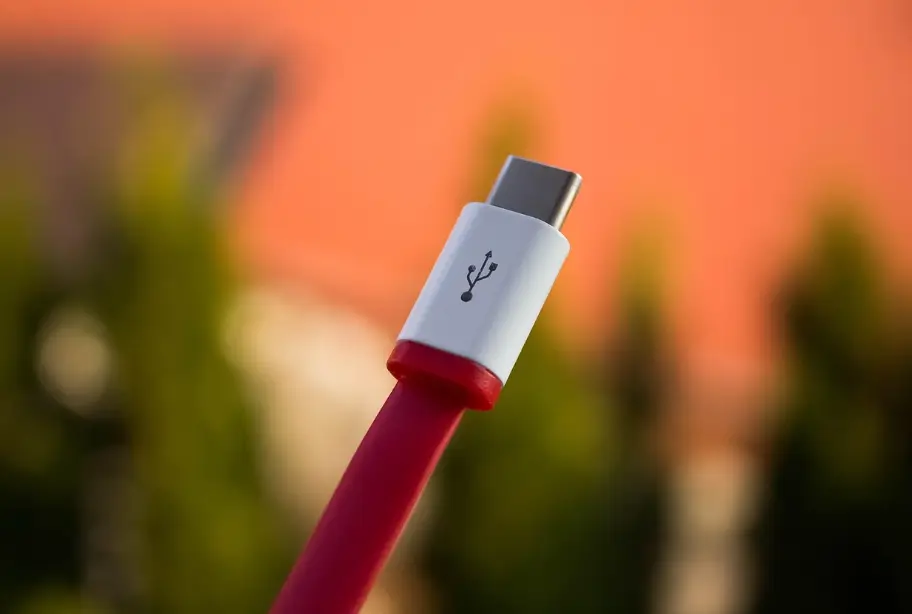
If you have any questions about adhesive selection and usage, please feel free to contact us. Our team of experts has extensive experience and can provide you with free consultation services.